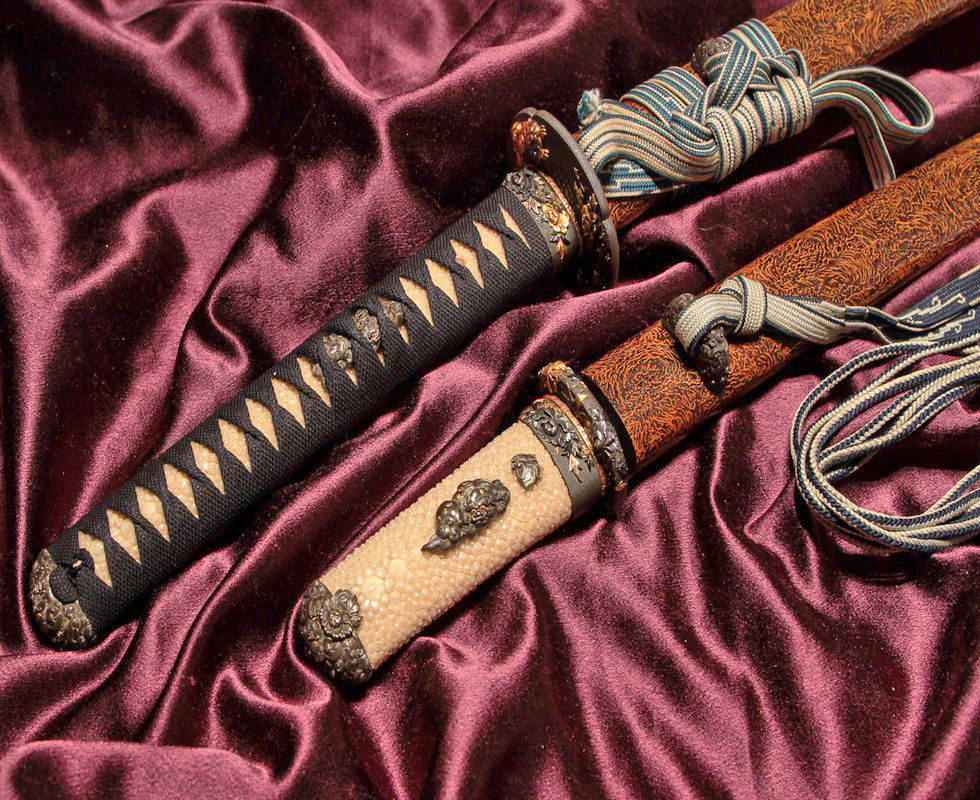
LES TYPES DE FORGEAGES DES SABRES JAPONAIS EN FONCTION DE LA NUANCE DES ACIERS
POURQUOI UNE LAME FORGÉE ?
C'est le processus de forge qui définit le type de lame de sabre. Les Katana ou sabres de Samourai authentiques étaient forgés à la main. Les lames forgées sont de bien meilleure qualité. La forge permet une meilleure répartition du carbone dans l'acier. Les forgerons ont la maîtrise nécessaire pour obtenir les meilleurs résultats. Chaque lame forgée main est également une pièce unique.
-
Étape 1: Forge
La forge consiste à marteler un ou plusieurs lingots d'acier carbone de manière à obtenir la forme de la lame. La forge à la main garantit la meilleure et égale dispersion du carbone dans tous l'acier afin de réaliser une excellente lame.
-
Étape 2: Mise en forme
La lame qui, à ce stade, n'est toujours pas trempée, est formée selon les dimensions exigées.
-
Étape 3: Trempe sélective traditionnelle par enrobage à l'argile
Pour obtenir un durcissement différentiel, le forgeron recouvre manuellement la lame avec une mélange d'argile spéciale, de charbon de bois et d'eau, d'épaisseurs différentes. Il faut très peu d'épaisseur d'argile sur le tranchant et plus d'épaisseur d'argile sur le reste de la lame de manière à obtenir un refroidissement différent suivant les zones et donc des duretés différentes. Celà permet d'obtenir un tranchant "Ha" très dur et un dos de la lame "Mune"moins dur, donnant à la lame une très bonne résistance aux chocs et un tranchant très résistant.
-
Étape 4: Trempe
À ce stade, un savoir-faire spécial est exigé. La lame est chauffée à une température prédéterminée et refroidie dans un bain d'eau. Cette étape déterminera le Hamon, le Sori et la rectitude de la lame. Le résultat dépend principalement de la compétence du forgeron.
-
Étape 5: Sori, point d'équilibre et point Monouchi
La courbure "Sori", le point d'équilibre et le point "Monouchi" seront déterminés en fonction de l'utilisation pour laquelle le sabre aura été forgé : réalisation de Kata, pratique du Tameshigiri ou du Battodo.
-
Étape 5: Le polissage
Le polissage est fait manuellement pour fournir une excellente finition et révéler la ligne de trempe "Hamon" ainsi que le grain et la structure de l'acier.
LES ACIERS
LE SHINGANE (Acier tendre) : C'est le coeur de la lame. Constitué d'acier, il est flexible et plie plutôt que de casser. Cependant, étant trop tendre, il ne pourrait constituer l'entière lame, qui ne trancherait pas. Il est aussi nommé "Shintetsu". La présence de shigane au coeur permet de donner à la lame son élasticité.
LE KAWAGANE (Acier intermédiare) : Il existe un grand nombre de lamination différentes combinant 2 ou 3 de ces métaux intermédiaires.
LE HAGANE (Acier dur) : Constitué d'acier, il est cassant mais très dur et tranchant. Il est souvent plié autour du Shigane. Aussi appelé "Uagane".
LES DIFFERENTS TYPES D'ASSEMBLAGES D'ACIERS POUR LA REALISATION D'UN LAME
On sait que les lames des sabres sont faites de laminages de plusieurs métaux différents, que ce soient des aciers durs (Hagane), des aciers intermédiaires (Kawagane) ou tendres (Shingane). En plus des lames réalisées avec un seul acier plié, les sabres japonais de haute qualité sont également composés de différentes couches distinctes de différents types d'acier (Plus ou moins durs). Cette technique de fabrication utilise différents types d'acier, pour accentuer les caractéristiques souhaitées dans différentes parties du sabre, au-delà du niveau offert par le traitement thermique différentielle (Trempe).
LES ASSEMBLAGES
Il y a presque un nombre infini de façons dont les aciers pourraient être assemblés, qui souvent varie considérablement d'un forgeron de forgeron. En général, le barre plus dure en acier est martelé, étirée et pliée en "U", puis l'acier de base très doux est inséré dans le "U". Ensuite, ils sont forgés et martelés pour les souder ensemble, tout en donnant la forme de base de la lame. À la fin du processus, les deux pièces d'acier sont fusionnées, mais conservent leurs différences de trempabilité. Les types de construction les plus complexes sont en général trouvé sur des lames anciennes, avec la grande majorité des armes modernes étant composé d'une section unique ou au plus deux ou trois sections. Une autre façon de procéder, est d'assembler les différentes pièces en un bloc, en les forgeant et en les soudent ensemble, puis étirer l'acier pour en faire une lame, de telle sorte que les différents aciers soient correctement répartis. Cette méthode est souvent utilisée pour les modèles complexes, elle permet d’avoir une lame avec laquelle, l’on peut parer sans crainte d'endommager le bord de la lame. Pour les types de Honsanmai ou Shihozume, des morceaux d'acier dur sont ajoutés à l'extérieur de la lame d'une manière similaire. Les types de Shihozume et Soshu sont assez rares.
LES DIFFÉRENTS TYPES DE FORGEAGES EN FONCTION DES NUANCES D'ACIERS
-
MARU : La grande majorité des Katana et Wakizashi modernes sont de type de Maru (Parfois aussi appelé Muku), c’est le type de lames le plus courant, ce sont des lames forgées uniquement en aciers durs. Ce sont des monoblocs de Hagane. C'est la composition la plus pauvre.
-
KOBUSE : Le type de lame Kobuse est faite en utilisant deux aciers, (Appelés Hagane : aciers de bord) et Shingane (Acier de base). ont un noyau d'acier doux, enveloppé sur les côtés et le tranchant par de l'acier très dur. Cette composition a été employée durant la Seconde Guerre Mondiale et est toujours utilisée.
-
HONSANMAI (Sanmai) : Pour les types Honsanmai on ajoute un troisième acier, (Kawagane : acier de la peau). Ces lames ont la composition la plus commune : 4 lingots, un noyau et le dos en acier doux, les côtés en acier dur, le tranchant en acier très dur.
-
TAMAHAGANE : La lame est forgée à partir de 2 types acier, le plus doux est placé au sein du plus durs. Cet art de forge issu du modèle japonais Tamahagane qui n'est enseigné, au Japon, qu'aux meilleurs forgerons et ceci depuis de siècles. Les deux aciers, forgés pliés (26000 feuilles) et trempés grâce à la technique d'enrobage traditionnel à l'argile, laissent apparaître des cristaux de martensite et le Hamon. Celui-ci n'est rendu visible sur les lames que par le poli manuel.
-
SOSHU KITAE : Sont des lames composées des différents aciers. Il y a 7 lingots et 3 densités d'aciers. On trouve un noyau en acier doux, la face interne des côtés en acier dur, le dos, la face externe des côtés et le tranchant en acier très dur. Masamune forgeait ses lames en Soshu-kitae. C'est le composite le plus complexe et un véritable exploit pour un forgeron.
-
SHIHOZUME : Les lames ont 5 lingots, un noyau en acier doux, le dos et les côtés en acier dur, le tranchant en acier très dur.
-
MAKURI : Les lames ont un noyau en acier doux enveloppé entièrement d'acier très dur.
-
WARIHA TETSU : Les lames ont le dos en acier dur, le tranchant en acier très dur (Généralement pour les Wakisashi et Tanto).
-
ORIKAESHI SANMAI : Les lames sont faites de 6 lingots.
-
GOMAI : Les lames ont un noyau en acier très dur, une enveloppe interne en acier doux, une enveloppe externe en acier très dur.
LES PRINCIPAUX TYPES DE FORGEAGE
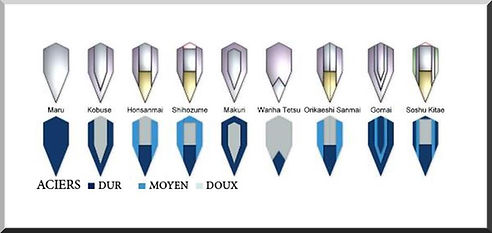





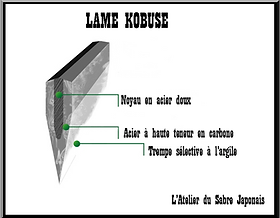
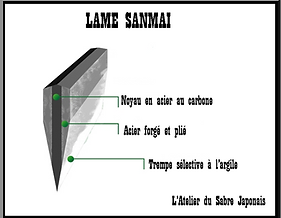
